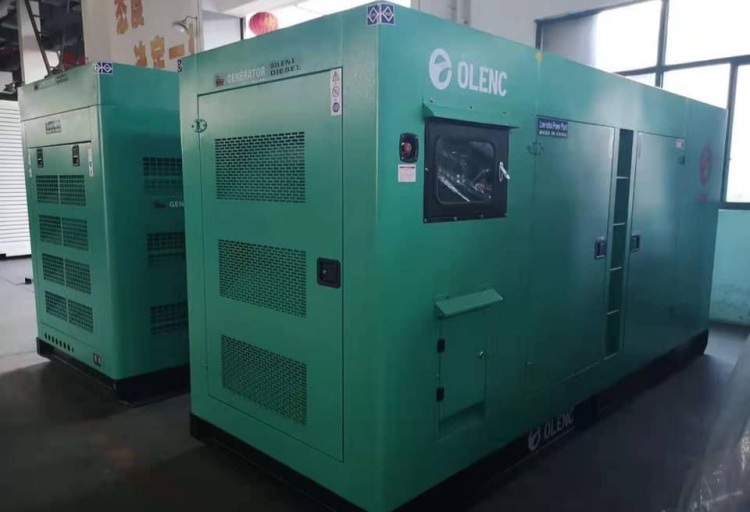
The negative impact of diesel emissions
Diesel particulate matter (PM) consists of black carbon, or soot, along with various organic compounds. Diesel exhaust also releases gaseous pollutants, including volatile organic compounds (VOCs) and nitric oxides (NOx). The emission of NOx from diesel engines is significant because it can undergo chemical reactions in the atmosphere, leading to the formation of particulate matter and ozone. Additionally, diesel exhaust contains carbon dioxide (CO2).
Accurately quantifying the exact amount of PM generated by diesel engines annually is a complex task due to variations in engine type, fuel type, and operating conditions. However, according to estimates, diesel engines globally produce an astounding 1.3 billion tons of particulate matter each year.
Black carbon, a component of diesel PM, is a recognized carcinogen and is associated with the occurrence of strokes, heart attacks, and chronic respiratory diseases. The California Air Resources Board (CARB) estimates that diesel PM contributes to approximately 1,400 premature deaths from cardiovascular disease annually in California alone. Furthermore, a study conducted in 2022 even found a correlation between low-level exposure to PM and behavioral issues, as well as lower IQ scores in children aged 2 to 4 years.
Ensuring clean air to breathe is a crucial social determinant of health and should be regarded with the same significance as access to education, nutritious food, employment opportunities and adequate shelter.
The role of diesel particulate filters (DPFs) in mission-critical facilities
DPFs are crucial tools for reducing emissions from diesel engines. These exhaust after-treatment devices effectively trap and remove PM from exhaust, helping to prevent harmful emissions from entering the air. DPFs can be fitted to various engines, including backup generators used in mission-critical facilities. The cleaning process, known as regeneration, ensures that captured PM is removed from the filter, maintaining optimal performance.
Active vs. passive regeneration
There are two types of diesel particulate filters: active and passive. Passive filters rely on the heat of combustion to regenerate and burn off trapped soot. However, in cases where generators experience intermittent demand, such as standby units in data centers, passive filters may not efficiently perform their cleaning function. This can result in clogged filters and reduced performance during power outages. On the other hand, active filters undergo self-cleaning during normal engine operation, independent of exhaust temperatures. This flexibility ensures maximum efficiency and reduces the need for additional measures like costly generator load banks.
Meeting sustainability goals through exhaust aftertreatment
Emissions regulations have been steadily increasing, with California at the forefront of these efforts. Mission-critical facilities, which often house multiple generator units in a compact area, face unique challenges in meeting these regulations.
To meet regulatory standards and achieve significant reductions in emissions and maintenance workloads, a data center on the west coast in Santa Clara, California, successfully installed 25 active diesel particulate filters onto the existing MTU S4000 engines.
“When you have facilities with 30 to 50 units, multiplied across several facilities in a geographic area, the concern for regulation ramps up, especially when there are existing neighborhoods or communities in that area,” said Roberto Montero of Rypos, a manufacturer of diesel exhaust aftertreatment filters.
The proximity of these facilities to existing communities further emphasizes the need to reduce diesel engine emissions. By prioritizing compliance and sustainable practices, mission-critical facilities can demonstrate their commitment to environmental responsibility and community well-being. Manufacturers of aftertreatment solutions play a vital role in helping facilities reduce emissions. By providing emissions reduction data based on generator specifications, these manufacturers assist consulting engineers, facility design teams, and ESG/EHS groups in making informed decisions. Training and educational resources are crucial in ensuring seamless operation of exhaust aftertreatment systems, empowering staff to utilize these technologies effectively.
News source: https://www.rypos.com/resources/emissions-blog/clearing-the-air/